Warranty and Certification Testing
Ensures System Performance
Certification verifies that cabling meets performance standards, ensuring reliable network operation.
Required for Warranty
Most manufacturers, including DINTEK Electronics, mandate certification for warranty coverage.
Prevents Future Failures
Testing detects installation errors or damage, reducing costly repairs down the line.
Protects Installer Reputation
Certification provides proof that the installation was done correctly, safeguarding both the installer and end user.
Certification Testing
DINTEK Electronics, like other leading cabling system manufacturers, requires certification testing to ensure the cabling plant performs as promised. Without it, warranties aren’t granted, which could lead to long-term risks and a poor return on investment (ROI).
What is certification testing? Certification testing is the process of verifying that data cabling installations meet industry performance standards. These standards are typically set by organizations such as the Telecommunications Industry Association (TIA), International Organization for Standardization (ISO), and Institute of Electrical and Electronics Engineers (IEEE). Certification testing is carried out by specialized testing devices, often referred to as cable testers or certifiers, that measure various parameters to determine if the cabling meets performance benchmarks for speed, reliability, and bandwidth.
Key parameters in certification testing:
- Wiremap – Ensures that all pairs of cables are correctly wired and connected.
- Propagation Delay – Measures how long it takes for a signal to travel through the cable.
- Attenuation – Determines the loss of signal strength over a given distance.
- Attenuation to crosstalk ratio (ACR-N) – Determines the remaining bandwidth of the cable after taking attenuation and crosstalk into account.
- Crosstalk (NEXT and FEXT) – Assesses the interference between wire pairs.
- Return Loss – Measures the amount of signal reflected back to the source due to impedance mismatches.
- Insertion Loss – Tests how much signal is lost during transmission through the cable.
Certification testing is typically performed after installation and before the network is fully operational. Successful certification is often required by industry standards, project specifications, and warranty agreements.
What is a Data Cabling Warranty?
A data cabling warranty is a guarantee provided by the cabling manufacturer that ensures the performance and longevity of the installed cables. These warranties typically last 15 to 25 years and cover the performance of the cabling system under normal operating conditions.
- Product Warranty: Covers manufacturing defects in the cable and connectivity components (e.g., jacks, panels, and patch cords).
- System Warranty: Ensures that the entire cabling system, including design and installation, will perform up to the required standards for a specified period.
- Application Assurance Warranty: Guarantees that the cabling infrastructure will support specific network applications, such as 10G Ethernet, for the duration of the warranty.
Why are Warranty and Certification Testing Critical?
Although a structured cabling system accounts for only a fraction of total network costs, it plays an essential role in connecting devices and transmitting data. It’s also one of the most disruptive and expensive components to replace. That’s why leading manufacturers like DINTEK Electronics offer warranties that not only cover individual component defects but also guarantee system performance over the cabling’s lifecycle.
DINTEK’s system warranties typically last 25 years, ensuring that the installed cabling system can support multiple generations of equipment. For installers, offering a system warranty is a mark of distinction, demonstrating their expertise and commitment to quality. For end users, it offers the assurance that the system will remain reliable and high-performing over time.
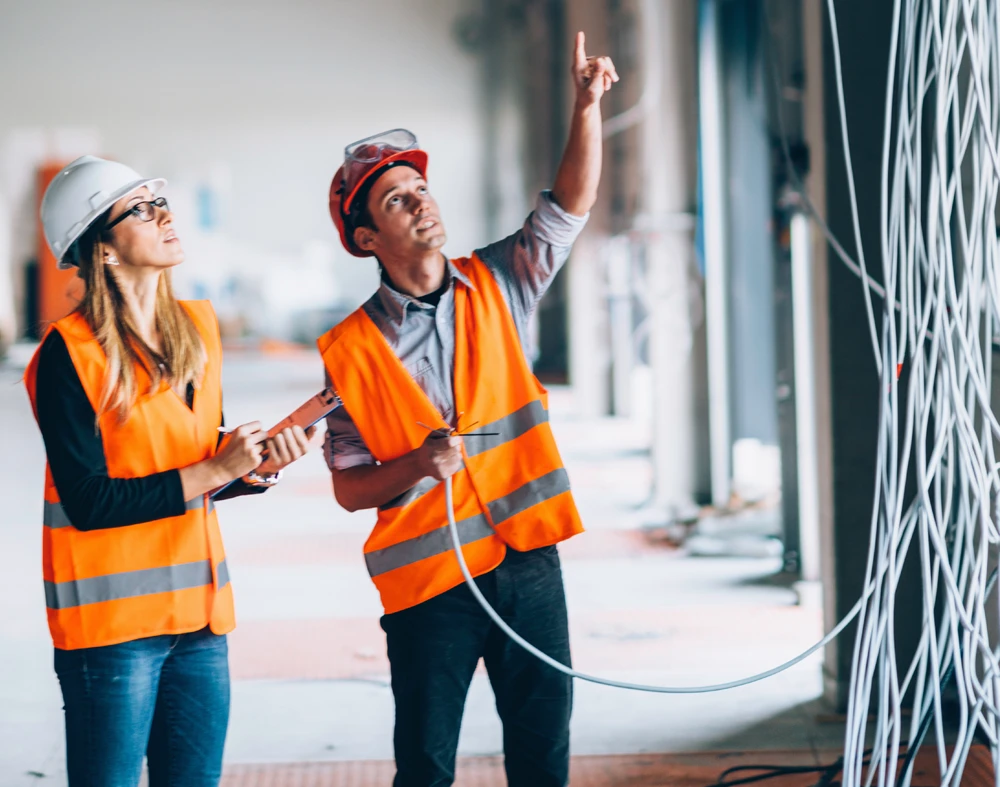
“Being told by a manufacturer that a product is high quality is well and good, but how can you know for sure unless the manufacturer is willing to stand behind their products and back that up”
Obtaining a Warranty
To activate a cabling warranty, certification testing is a critical step typically required by the manufacturer. Most manufacturers will only honor the warranty if the cabling system has been installed by a certified contractor and if the installation passes certification testing based on recognized industry standards. This ensures that both the client and the manufacturer are protected, confirming that the cabling system has been correctly installed and will perform as expected over its lifespan.
The process of securing a warranty begins with hiring a certified installer, as manufacturers require that the installation be carried out by professionals who are trained and accredited to meet their specific quality standards. Once the installation is complete, certification testing must be conducted using specialized equipment designed to evaluate each cable run. These tests assess critical parameters such as signal loss, crosstalk, and attenuation, verifying that the cabling meets the required performance benchmarks.
Once testing is complete and the system passes all necessary checks, the results are submitted to the manufacturer. This step is essential, as the manufacturer needs to review and verify the certification results before issuing the warranty. Upon successful verification, the manufacturer will provide a warranty that guarantees the performance and reliability of the cabling system for the specified term, offering long-term protection for the client.
DINTEK Electronic doesn't issue warranties lightly
DINTEK recognizes that investing in network infrastructure is a significant decision, and ensuring the long-term reliability of such investments is essential. To support this, DINTEK offers a robust and comprehensive 25-Year Warranty System, reflecting the company's commitment to quality, durability, and customer satisfaction.
DINTEK provides two types of warranties: the 25-Year Product Warranty and the comprehensive System Warranty. The 25-Year Product Warranty guarantees that covered products are free from physical defects and, with normal and reasonable usage, will continue to function for up to 25 years from the date of purchase.
For more information on the DINTEK 25-Year Warranty, click HERE.
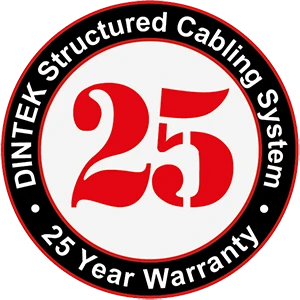
- products
- standards
- installation
- performance